Profiling
In fabrication, a profile consists of the more or less complex outline of a shape to be cut in a sheet of material such as laminated plastic, aluminum alloy or steel plate. In modern practice, a drawing office determines the shape and dimensions required to fit the sheet into a larger work and feeds directions to a computer controlling a profile cutter. This then cuts the shape from a standard-sized sheet. The cutting head may use a rotating cutter like that of a spindle router or (in the case of steel plate) a torch which burns oxy-acetylene or other oxy-gas.
Plasma Cutter Configuration
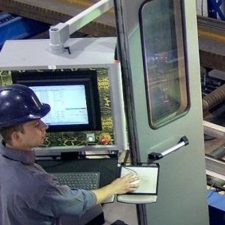
Plasma Cutting Process
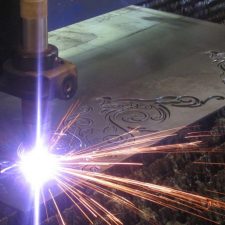
Plasma Cut Product
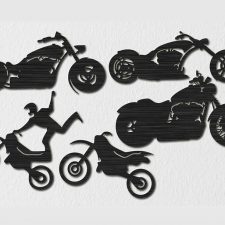
Multi-head oxy fuel profiling for plates up to 300mm thick
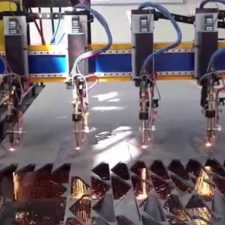
- Saw Cutting
- Miter Cutting
- Cut and Roll Grooving
- Flame Cutting
- Mechanical Torch Cutting – beveled or square cut ends
- Laser Cutting
- Plasma Cutting
Coating & Finishing
Coating, Wrapping and Lining
Functional coatings may be applied to change the surface properties of the metal, such as adhesion, water-proofing, corrosion resistance or wear resistance.
Blast, Clean and Paint Capabilities
Abrasive blasting forcibly propels a stream of material against a surface under high pressure to smoothen or roughen surfaces, shape a surface or remove surface contaminants. Cleaning is the first stage treatment before the application of any coating. Surface contaminants on the steel surface, such as oil and grease must be removed before the process.
Painting Process
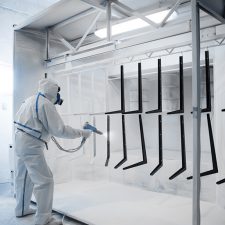
Air Blasting
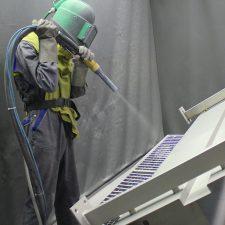
Wheel Blasting
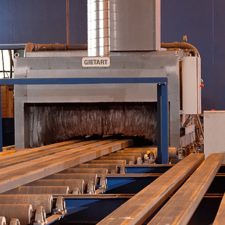
Wheelblast Machines

Shot Blasting
Wheel Blasting
Wheel blasting directly converts electric motor energy into kinetic abrasive energy by rotating a turbine wheel. The capacity of each wheel goes from approximately 60kg/min up to 1200kg/min. With these large amounts of accelerated abrasive, wheelblast machines are used where big parts or large areas of parts have to be derusted, descaled, deburred, desanded or cleaned.
Air Blasting
Air blast machines can take the form of a blastroom or blast cabinet. The blast media is pneumatically accelerated by compressed air and projected by nozzles onto the component. The blasting task determines the choice of the abrasive media, in most cases any type of dry or free running abrasive media can be used.
Coating & Finishing
Cement Lining
Internal cement lining assures anti-corrosion protection and stability of hydraulic parameters of pipelines for water and sewages. Some advantages of cement lined steel pipes and fittings are resistance to corrosion and various oxidizing agents, e.g. ozone, chlorine, very high abrasion resistance allowing high flow rate of fluids and full resistance of cement lining to plastic of strain of the steel pipes.
Threading
Threading is the process of creating a screw thread. There are many methods of generating threads, including subtractive methods (thread cutting and grinding), deformative or transformative methods (rolling and forming, molding and casting) and additive methods (such as 3D printing).
Cement Lining
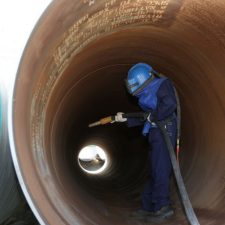
Threading
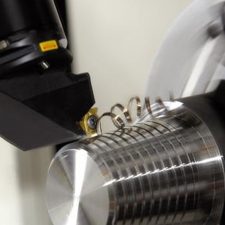
Galvanising Process
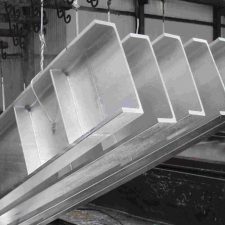
Pickling & Oiling
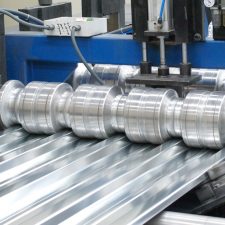
Galvanising Process Pickling & Oiling
Galvanising
Galvanization is the process of applying a protective coating to steel or iron to prevent rusting. Galvanizing protects as it forms a coating of corrosion-resistant zinc which prevents corrosive substances from reaching the more delicate part of the metal. Even if the coating is scratched, the exposed steel will be protected by the remaining zinc.
Pickling & Oiling
Pickling is metal surface treatment used to remove impurities, such as stains, inorganic contaminants, rust or scale from various metals. A solution called pickle liquor, which contains strong acids, is used to remove the surface impurities. To protect metals from rusting, they are provided with a uniform coating of special rust preventive oil. This also guards against atmospheric corrosion and allows for a longer storage period.
Bespoke Products & Special Fittings
We are able to help industries with their needs that cannot be satisfied by conventional means. With our vast expertise and precise manufacturing and fabricating capabilities, we have customers who come to us with highly-specific needs in fabrication and custom-made products.
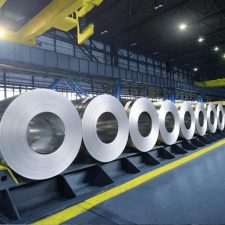
Plate Rolling Process
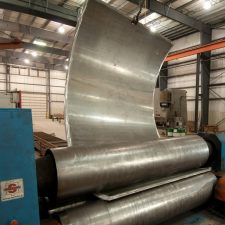
Customised Fabrication
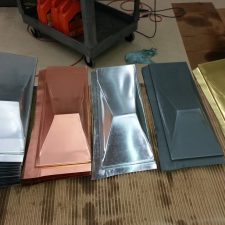
Steel Bending
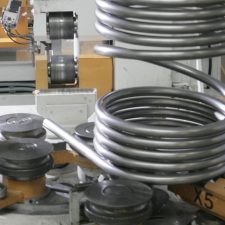
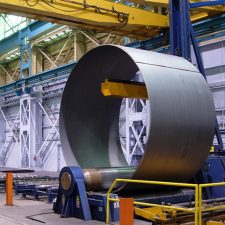
Plate Rolling Machine
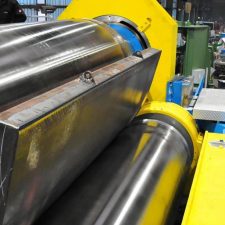
Steel Bending Machine
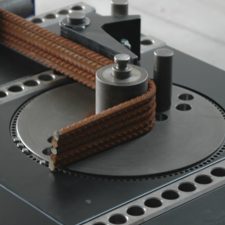
Testing
- Positive Material Identification
- X-Ray: Weld Seam, Full-Body UT testing
- The Drop Weight Tear Test (DWTT)
- Charpy Impact Testing
- Vickers Hardness Test
- Brinell Hardness Test
- Rockwell Hardness Test
- Hydrogen Induced Cracking Test (HIC)
- Through Thickness Property Test (TTP)
- Ultrasonic Thickness Testing (UTT)
- Strain-Aged Testing
- Tensile Test
Charpy Impact Test
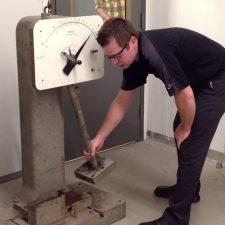
Tensile Test
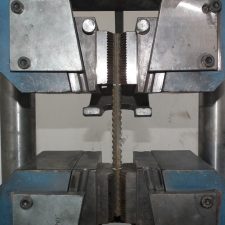
Brinell Hardness Test
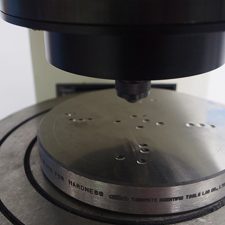
Rockwell Hardness Test
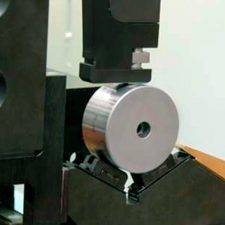
Vickers Hardness Test
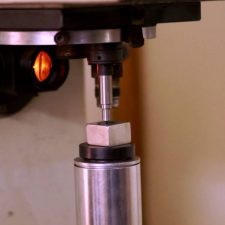
Rockwell Hardness Test Vickers Hardness Test
Hardness Testing System
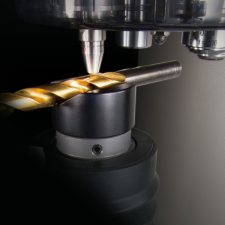
Our customers rely on metal testing and material analysis to provide the test results, certified reports and answers they need to run their business. Our engineers and technicians can verify the quality of raw materials or end products, help research product failures and provide the metal test services that is needed to meet industry and customer requirements.
Logistics
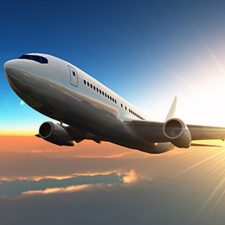
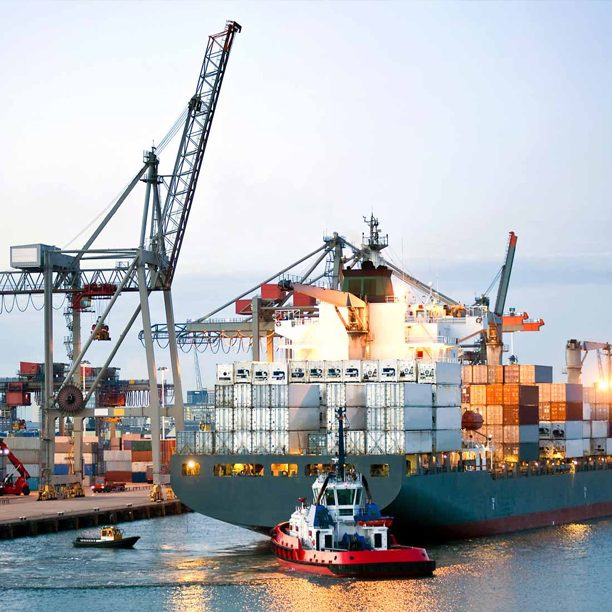
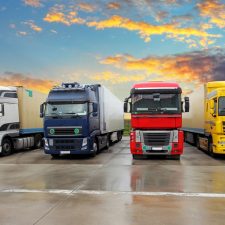
Sea Logistic
Air Logistic
Land Logistic
Our logistics management plans, implements and controls the efficient and effective flow and storage of goods and services between the point of origin and the point of consumption in order to meet customer’s requirements.
Be it materials management, channel management, distribution through the various modes of freight transportations, we are there to assist you.